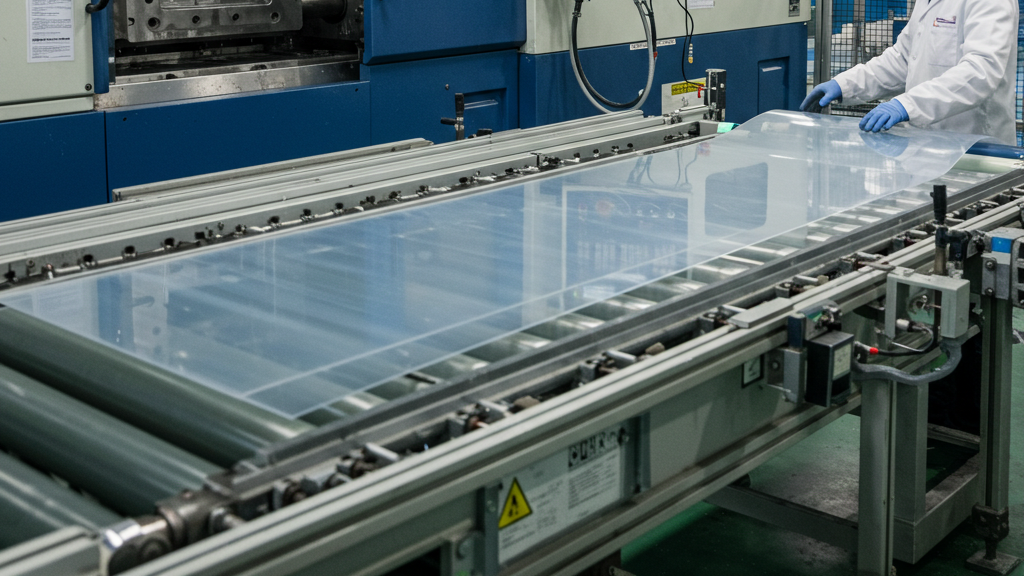
Polycarbonate (PC) sheets are widely used, but the flatness of the injection molding process is crucial. Subtle changes in process parameters can affect the flatness of the final product. Internal stress, cooling uniformity, and mold design are all potentially critical factors.
The injection molding process is complex, and the flatness of PC sheets is susceptible to various influences. From the injection of molten plastic to cooling and forming, each step is critical. So, what specific process parameters affect the flatness of PC sheets? We will focus on core elements such as injection speed, melt temperature, holding pressure, and cooling system design to analyze how they affect the flatness and final shape of PC sheets.
Which Injection Molding Parameters Directly Affect PC Sheet Flatness?
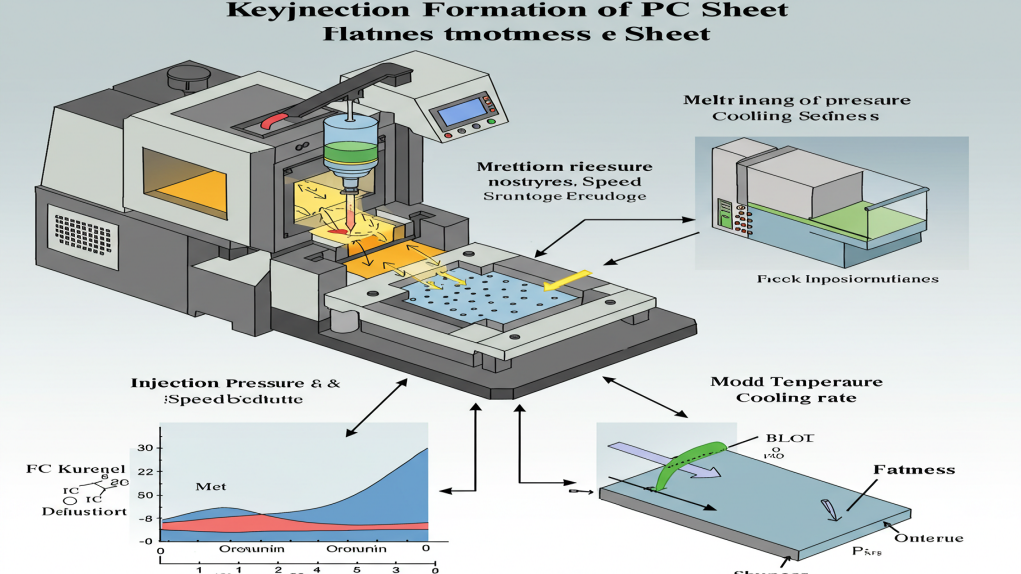
In the injection molding of polycarbonate (PC) sheets, not all process parameters have an equal impact on the flatness of the final product. Some key parameters act like precise control knobs, directly determining the flow, cooling, and solidification of the molten plastic, thus significantly influencing the flatness of the PC sheet.
- Melt Temperature: Inappropriate melt temperature can affect PC sheet flatness due to differences in flowability or shrinkage.
- Injection Pressure and Speed: Improper injection parameters can cause flow instability and internal stress, leading to deformation of the PC sheet.
- Holding Pressure and Time: Inadequate holding pressure makes it difficult to compensate for shrinkage, affecting the final flatness of the PC sheet.
- Mold Temperature and Cooling Rate: Poor mold temperature and cooling control can affect the internal stress and flatness of the PC sheet.
How do these parameters affect flatness issues at the microscopic level?
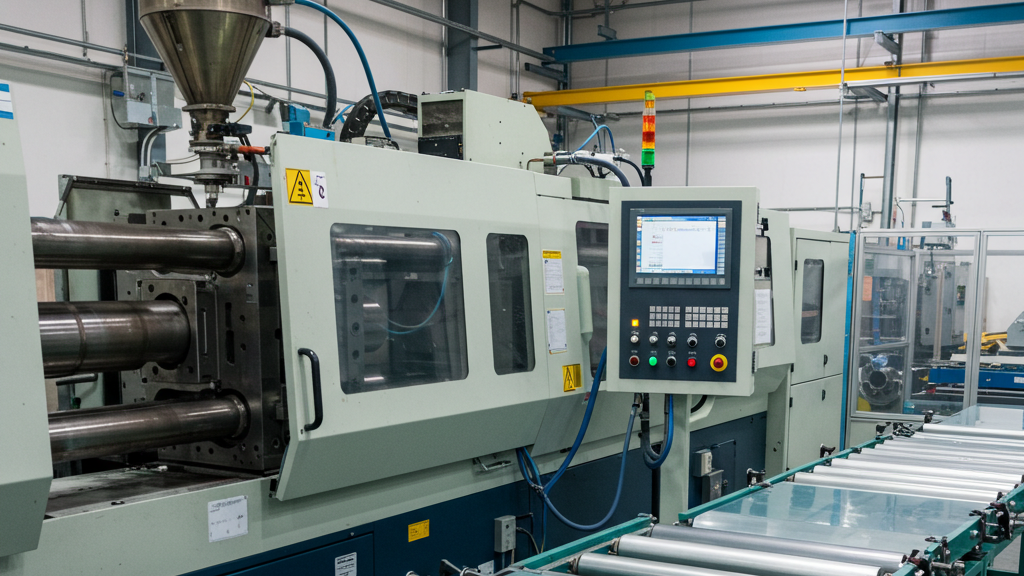
These seemingly macroscopic flatness defects, such as warpage and deformation, are often rooted in subtle differences in molecular behavior at the microscopic level. Exploring how injection molding parameters precisely control these microscopic behaviors will help us fundamentally understand and solve the flatness problems of PC sheets.
- Melt Temperature: Inappropriate melt temperatures affect the movement of molecular chains and the uniformity of cooling shrinkage, influencing the flatness of PC sheets at the microscopic level.
- Injection Pressure and Speed: Unsuitable injection parameters lead to unstable melt flow and differences in molecular chain orientation, thereby affecting the flatness of PC sheets at the microscopic level.
- Holding Pressure and Time: Insufficient or excessive holding pressure can cause internal defects and stress concentration, affecting the flatness of PC sheets at the microscopic level.
- Mold Temperature and Cooling Rate: Uneven mold temperature and cooling rate can cause differences in crystallinity and shrinkage rate, leading to flatness problems in PC sheets at the microscopic level.
What are the differences of injection optimization strategies for PC boards?
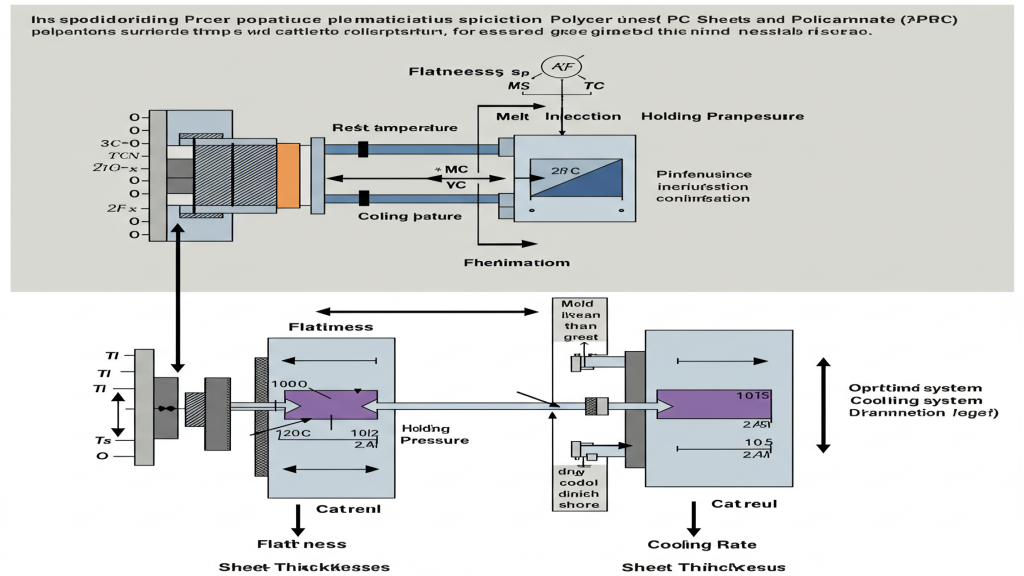
Polycarbonate (PC) sheets come in various specifications, with different thicknesses and sizes. This means that during injection molding, the optimization strategies for flatness need to be tailored to the specific material for different specifications of sheets. A universal set of parameter settings often cannot meet the strict flatness requirements of all PC sheet specifications.
- Thinner and smaller PC sheets: Focus on controlling injection speed and pressure to ensure rapid and uniform filling and cooling.
- Thicker but smaller PC sheets: The key is to ensure sufficient filling and uniform, slow cooling to reduce internal stress.
- Thinner but larger PC sheets: The focus is on ensuring long-flow filling, optimizing injection parameters, and vent design.
- Thicker and larger PC sheets: Comprehensive optimization of filling, holding pressure, and cooling is required, and mold design is critical.
Main points of flatness control of PC board injection molding
Specification |
Key Parameters |
Optimization |
Microscopic Impact |
Flatness Impact |
Thin & Small | Injection Speed/Pressure/Cooling Rate | Fast & Uniform Filling/Cooling, Reduce Internal Stress | Reduced Flow Marks/Molecular Orientation Differences | Reduced Deformation/Unevenness |
Thick & Small | Holding Pressure/Cooling Time | Sufficient Filling/Slow & Uniform Cooling, Compensate Shrinkage | Reduced Voids/Stress Concentration/Shrinkage Differences | Reduced/Warpage |
Thin & Large | Injection Control/Gating/Venting | Ensure Long Flow Filling, Reduce Resistance/Trapped Air | Ensured Melt Flow/Reduced Shear/Molecular Disorder | Reduced Insufficient Filling/Uneven Shrinkage Deformation |
Thick & Large | Phased Injection/Holding Pressure/Cooling/Mold Design | Comprehensive Optimization of Filling/Holding/Uniform Cooling/Mold Flow | Reduced Internal Stress/Crystallization/Shrinkage Differences | Maximum Reduction of Warpage/Deformation/Unevenness |
The impact of mold design on the flatness of PC sheets
Mold design is a crucial factor influencing the flatness of PC sheets. A reasonable mold structure can ensure uniform flow and filling of molten plastic within the cavity, avoiding internal stress caused by poor flow or uneven pressure distribution. The design of the cooling system is particularly important; uniform and efficient cooling can reduce inconsistent shrinkage caused by differences in cooling rates, thereby reducing the risk of warpage and deformation.
1.Feed System Design: A reasonable feed system ensures uniform mold filling, reduces internal stress, and is beneficial for PC sheet flatness.
2.Cooling System Design: Uniform and efficient cooling reduces shrinkage differences, lowers warpage, and ensures PC sheet flatness.
3.Vent System Design: Good venting avoids trapped air defects, ensuring the surface and overall flatness of the PC sheet.
4.Mold Structure and Precision: High rigidity and precision of the mold ensure cavity stability and flatness, directly affecting the flatness of the PC sheet.
Conclusion
In summary, the flatness of polycarbonate (PC) sheets during injection molding is complexly influenced by a variety of factors. Key injection molding parameters, such as melt temperature, injection pressure and speed, holding pressure and time, and mold temperature and cooling rate, ultimately determine the macroscopic flatness of PC sheets by controlling the movement, arrangement, and formation of internal stresses of PC molecular chains at the microscopic level.
For expert assistance in implementing for your production needs, visit our resource center or contact us. Let’s help you scale up your manufacturing with precision and efficiency!
Post time: Apr-15-2025